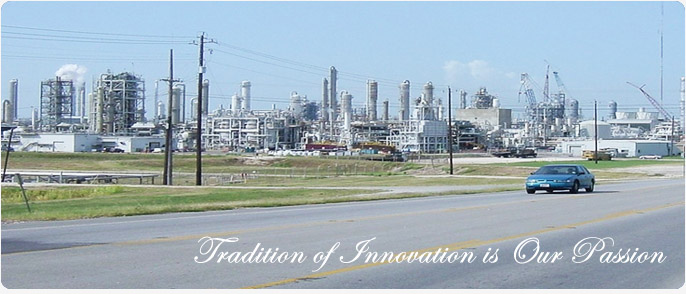
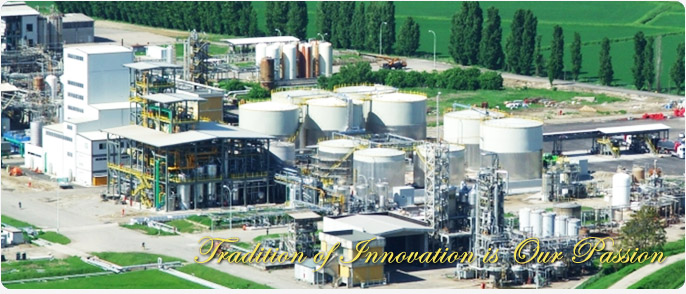
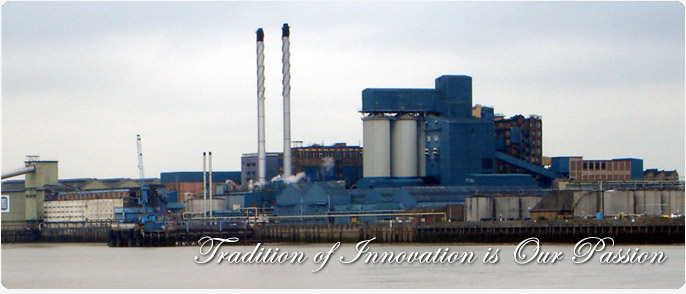
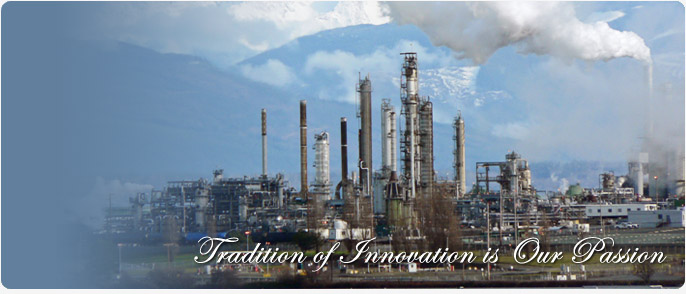
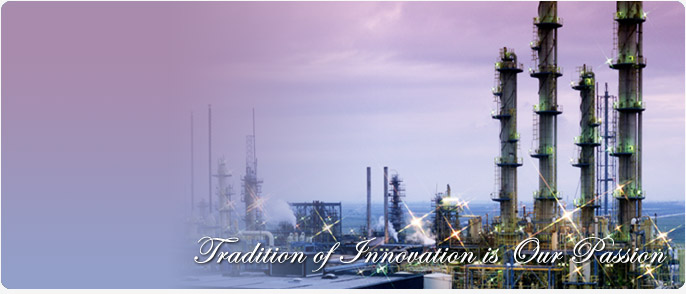
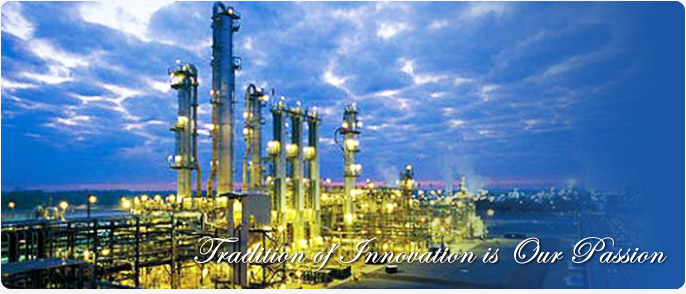
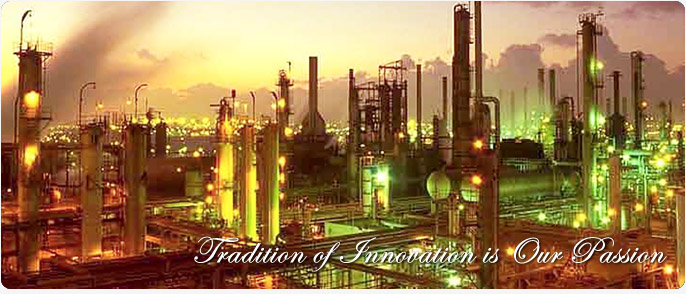
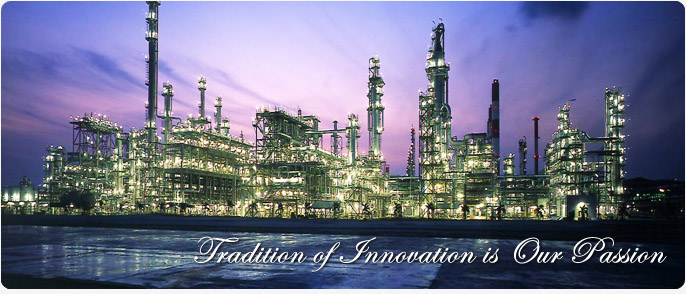
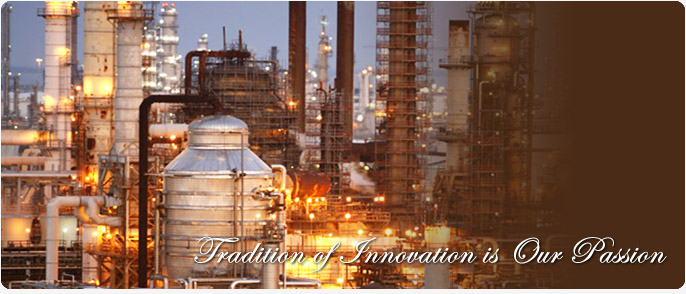
Integration of model, optimization, synthesis and control processes in industrial systems
4 January 2011
Background:
Operator Training Simulator (OTS) is application sofware developed for educating and training the process operators. OTS enables the trainees to understand the best operating practice with care, safety, and incident free working of a unit process. It addresses the operation of various condition, including emergency operation, start-up and shut-down operation, and problems associated with plant operation. Hence, current OTS contains various models engaging all aspects concerning the operation of a process unit in a real plant in the form of softwares and hardwares.
Operator Training Simulator (OTS)
In chemical process industries, a unit process usually comprises a train of the process equipments namely pumps, compressors, heat exchangers, furnaces, vessel, reactors, piping system, valves, instrumentation, etc. Operation of a unit process is managed by a control system equipment. There are numerous types of system control available, ranging from those utilizing traditional pneumatic signal system to the most sophisticated ones employing digital technology, such as Digital Control System (DCS). The control system used in this project is DCS. DCS consists of two main stations, Control Station and Operator Station. Control Station performs the control algorithm (including the other data handling) and Operator Station is a panel where the operator manage the unit process. To ensure the safety of the process operation, a unit process is provided with the interlock equipment. Despite that the operation of a unit process is generally controlled through the control panel (Operator Station) in the Control Room, a number of activities, such as turning on pumps and compressor, operating valves, and checking local instruments, are also manipulated by the field operator.
INSCITRON
PSE research group UGM has successfully developed a dynamic model of the OTS with an integrated development model, optimization, synthesis and control processes in industrial systems that namely as INSCITRON. Systematics of INSCITRON consists of the main server, data base server that serves to calculate and store data. Besides, there are instructor station and the engineer / operator station that is connected to the switch as shown in Figure 1.
Figure 1. Systemtic of INSCITRON
The role of specialized hardwares denoted on the scheme are:
1. Simulation Server (main server):
- To run the algorithms of the process simulation
- To govern the OPC Communication
2. Database server:
- To save all the simulation data
3. Computer instructor/ Administrator:
- To control and monitor the process simulation
- To execute the function of the instructor application
- To carry out the function of I/O of the process simulation
4. Computer operator:
- To run the function of the I/O of the process simulation
Display of INSCITRON
![]() |
![]() |
Figure 2a. Display of INSCITRON
![]() |
![]() |
Figure 2b. Interlock system of INSCITRON
Advantages of INSCITRON
INSCITRON use principles of chemical engineering tools (mass balance, heat balance, equlibrium and rate processes) for process model, so the developing model is a dynamic model. From the discussion with some experts as a user, they said that INSCITRON has several advantages such as:
- It can be functioned as an OTS for studying the phenomenon and characteristics in the startup process, normal operation, shutdown, emergency and mulfuction.
- It can be used to study the "know-how" existing processes in each unit operation.
- It can be used to study characteristic of product specifications when changes in raw material.
- It can be used to innovate the process by varying the design process variables (plant capacity, energy availability, operating conditions etc.).
- It can be used for process & energy audit and optimization by the process engineer (PE).